วัตถุประสงค์ของวัสดุเคลือบผิว
การเคลือบพื้นผิวภายนอกของท่อเหล็กเป็นสิ่งสำคัญในการป้องกันสนิม สนิมบนพื้นผิวของท่อเหล็กอาจส่งผลต่อการใช้งาน คุณภาพ และรูปลักษณ์ของท่อได้อย่างมาก ดังนั้น กระบวนการเคลือบจึงส่งผลกระทบอย่างมากต่อคุณภาพโดยรวมของผลิตภัณฑ์ท่อเหล็ก
-
ข้อกำหนดสำหรับวัสดุเคลือบผิว
ตามมาตรฐานที่กำหนดโดยสถาบันปิโตรเลียมแห่งอเมริกา ท่อเหล็กควรต้านทานการกัดกร่อนได้อย่างน้อยสามเดือน อย่างไรก็ตาม ความต้องการระยะเวลาป้องกันสนิมที่ยาวนานขึ้นได้เพิ่มขึ้น โดยผู้ใช้จำนวนมากต้องการความทนทานเป็นเวลา 3 ถึง 6 เดือนในการจัดเก็บกลางแจ้ง นอกเหนือจากข้อกำหนดด้านอายุการใช้งานแล้ว ผู้ใช้ยังคาดหวังว่าสารเคลือบจะรักษาพื้นผิวให้เรียบเนียน กระจายสารป้องกันการกัดกร่อนอย่างสม่ำเสมอโดยไม่มีการหยดหรือขาดซึ่งอาจส่งผลต่อคุณภาพภาพ
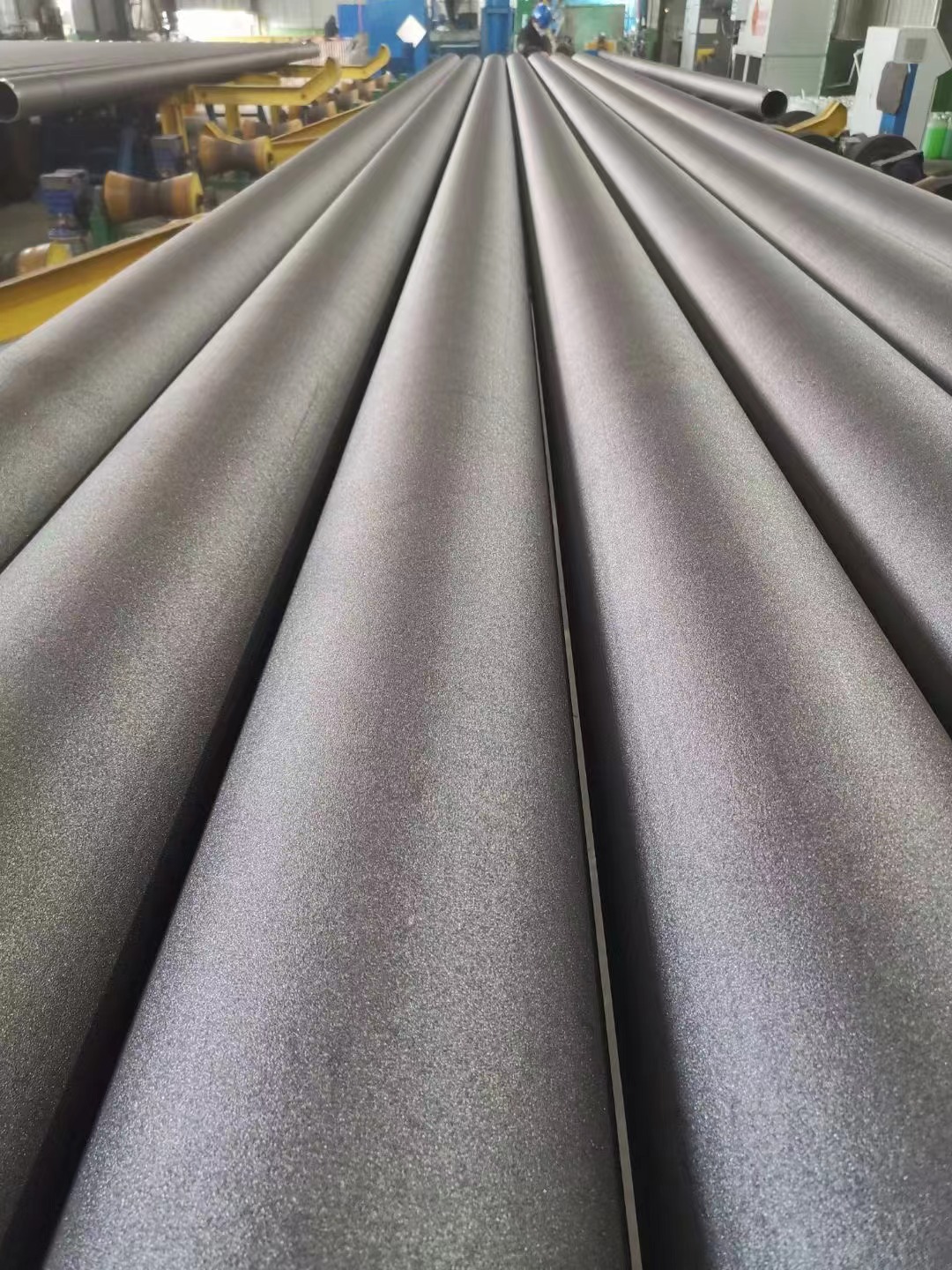
-
ประเภทของวัสดุเคลือบผิวและข้อดีข้อเสีย
ในเครือข่ายท่อใต้ดินในเมืองท่อเหล็กมีการใช้กันอย่างแพร่หลายในการขนส่งก๊าซ น้ำมัน น้ำ และอื่นๆ สารเคลือบท่อเหล่านี้ได้พัฒนาจากวัสดุแอสฟัลต์แบบดั้งเดิมไปเป็นเรซินโพลีเอทิลีนและวัสดุเรซินอีพอกซี การใช้สารเคลือบเรซินโพลีเอทิลีนเริ่มขึ้นในช่วงทศวรรษ 1980 และด้วยการใช้งานที่หลากหลาย ทำให้ส่วนประกอบและกระบวนการเคลือบได้รับการพัฒนาอย่างค่อยเป็นค่อยไป
3.1 การเคลือบยางมะตอยปิโตรเลียม
การเคลือบด้วยปิโตรเลียมแอสฟัลต์ ซึ่งเป็นชั้นป้องกันการกัดกร่อนแบบดั้งเดิม ประกอบด้วยชั้นปิโตรเลียมแอสฟัลต์ เสริมด้วยผ้าไฟเบอร์กลาสและฟิล์มโพลีไวนิลคลอไรด์ป้องกันภายนอก การเคลือบด้วยปิโตรเลียมแอสฟัลต์ให้การกันน้ำที่ดีเยี่ยม ยึดเกาะกับพื้นผิวต่างๆ ได้ดี และคุ้มต้นทุน อย่างไรก็ตาม การเคลือบด้วยปิโตรเลียมแอสฟัลต์มีข้อเสียหลายประการ เช่น ไวต่อการเปลี่ยนแปลงของอุณหภูมิ เปราะบางเมื่ออุณหภูมิต่ำ และมีแนวโน้มที่จะเสื่อมสภาพและแตกร้าว โดยเฉพาะในสภาพดินที่มีหิน ทำให้ต้องใช้มาตรการป้องกันเพิ่มเติมและมีค่าใช้จ่ายเพิ่มขึ้น
3.2 การเคลือบอีพอกซีด้วยน้ำมันดินถ่านหิน
อีพ็อกซี่ทาร์ถ่านหิน ซึ่งทำจากเรซินอีพ็อกซี่และยางมะตอยถ่านหิน มีคุณสมบัติทนน้ำและสารเคมีได้ดี ทนต่อการกัดกร่อน ยึดเกาะได้ดี มีความแข็งแรงทางกล และมีคุณสมบัติเป็นฉนวน อย่างไรก็ตาม ต้องใช้เวลาบ่มนานกว่าหลังการใช้งาน จึงอาจเกิดผลกระทบจากสภาพอากาศในช่วงเวลาดังกล่าวได้ นอกจากนี้ ส่วนประกอบต่างๆ ที่ใช้ในระบบเคลือบนี้ต้องได้รับการเก็บรักษาเป็นพิเศษ ทำให้ต้นทุนเพิ่มขึ้น
3.3 การเคลือบผงอีพ็อกซี
การเคลือบผงอีพ็อกซีซึ่งเปิดตัวในช่วงทศวรรษ 1960 เกี่ยวข้องกับการพ่นผงไฟฟ้าสถิตบนพื้นผิวท่อที่ผ่านการบำบัดและอุ่นล่วงหน้า เพื่อสร้างชั้นป้องกันการกัดกร่อนที่หนาแน่น ข้อดีของการเคลือบผงอีพ็อกซี ได้แก่ ช่วงอุณหภูมิที่กว้าง (-60°C ถึง 100°C) การยึดเกาะที่แข็งแกร่ง ทนทานต่อการแยกตัวของแคโทดิก แรงกระแทก ความยืดหยุ่น และความเสียหายจากการเชื่อมได้ดี อย่างไรก็ตาม ฟิล์มที่บางกว่าทำให้เกิดความเสียหายได้ง่ายและต้องใช้เทคนิคการผลิตและอุปกรณ์ที่ซับซ้อน ซึ่งสร้างความท้าทายในการใช้งานภาคสนาม แม้ว่าจะเหนือกว่าในหลายๆ ด้าน แต่ก็ยังต่ำกว่าโพลีเอทิลีนในแง่ของการทนความร้อนและการป้องกันการกัดกร่อนโดยรวม
3.4 สารเคลือบป้องกันการกัดกร่อนโพลีเอทิลีน
โพลีเอทิลีนมีความทนทานต่อแรงกระแทกและความแข็งสูง รวมถึงทนต่ออุณหภูมิได้หลากหลาย โดยนิยมใช้กันอย่างแพร่หลายในพื้นที่หนาวเย็น เช่น รัสเซียและยุโรปตะวันตกสำหรับท่อส่ง เนื่องจากมีความยืดหยุ่นและทนต่อแรงกระแทกได้ดีเยี่ยม โดยเฉพาะที่อุณหภูมิต่ำ อย่างไรก็ตาม ยังคงมีความท้าทายในการใช้งานกับท่อที่มีเส้นผ่านศูนย์กลางขนาดใหญ่ ซึ่งอาจเกิดรอยแตกร้าวจากความเค้น และน้ำที่ซึมเข้ามาอาจทำให้เกิดการกัดกร่อนใต้ผิวเคลือบ จึงจำเป็นต้องมีการวิจัยเพิ่มเติมและปรับปรุงเทคนิคการใช้และการใช้วัสดุ
3.5 การเคลือบป้องกันการกัดกร่อนแบบหนา
สารเคลือบป้องกันการกัดกร่อนชนิดเข้มข้นช่วยเพิ่มความทนทานต่อการกัดกร่อนได้อย่างมากเมื่อเทียบกับสารเคลือบมาตรฐาน สารเคลือบเหล่านี้มีประสิทธิภาพในระยะยาวแม้ในสภาวะที่รุนแรง โดยมีอายุการใช้งานเกิน 10 ถึง 15 ปีในสภาพแวดล้อมทางเคมี ทางทะเล และตัวทำละลาย และเกิน 5 ปีในสภาวะที่เป็นกรด ด่าง หรือเกลือ สารเคลือบเหล่านี้โดยทั่วไปจะมีความหนาของฟิล์มแห้งตั้งแต่ 200μm ถึง 2000μm ช่วยให้มั่นใจได้ถึงการปกป้องและความทนทานที่เหนือกว่า สารเคลือบเหล่านี้ใช้กันอย่างแพร่หลายในโครงสร้างทางทะเล อุปกรณ์เคมี ถังเก็บ และท่อส่ง
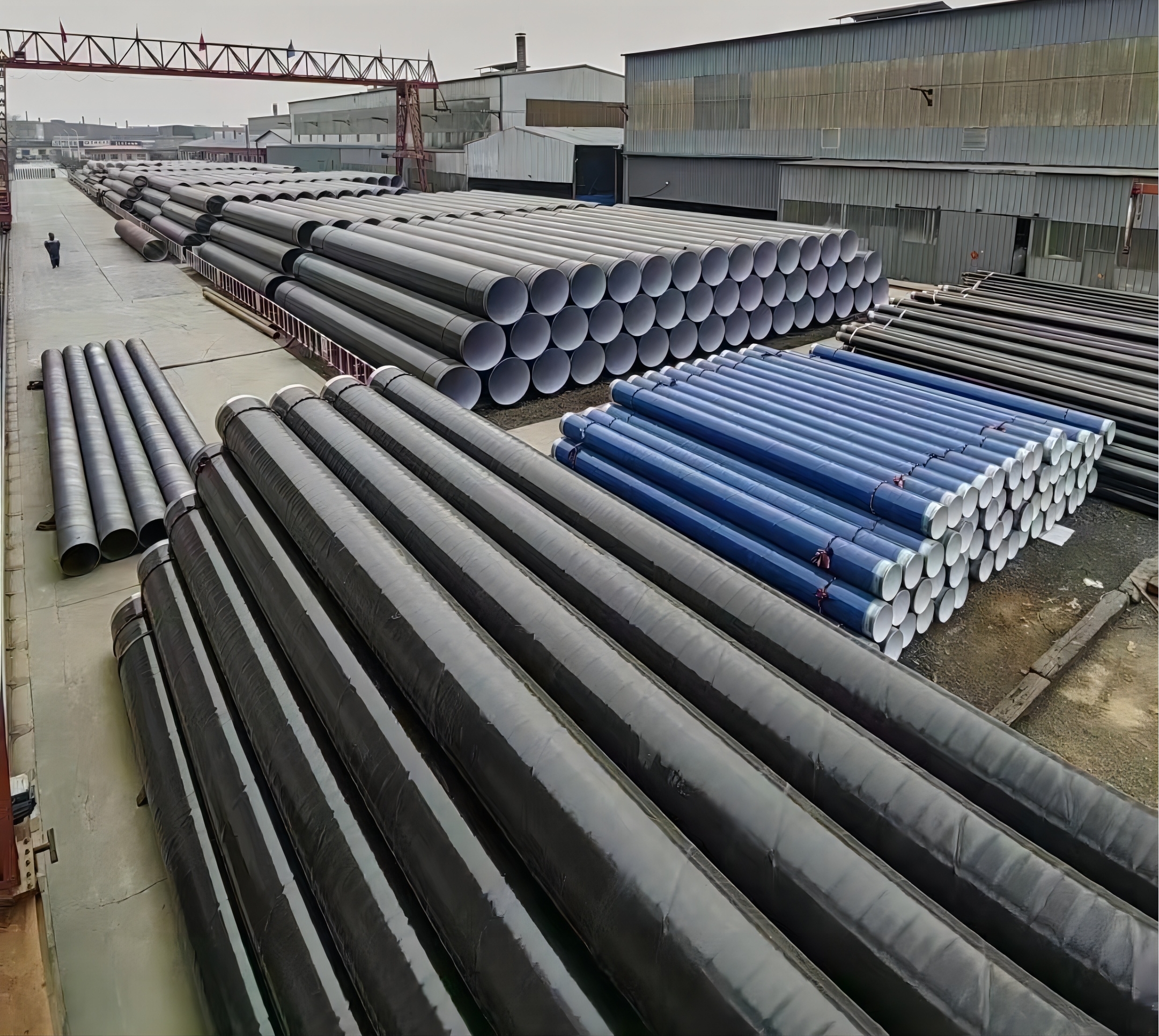
-
ปัญหาทั่วไปเกี่ยวกับวัสดุเคลือบ
ปัญหาทั่วไปที่เกิดกับการเคลือบ ได้แก่ การเคลือบผิวที่ไม่สม่ำเสมอ การหยดของสารป้องกันการกัดกร่อน และการเกิดฟองอากาศ
(1) การเคลือบที่ไม่สม่ำเสมอ: การกระจายตัวของสารป้องกันการกัดกร่อนที่ไม่สม่ำเสมอบนพื้นผิวท่อ ส่งผลให้เกิดพื้นที่ที่มีความหนาของการเคลือบมากเกินไป ส่งผลให้เกิดการสิ้นเปลือง ขณะที่พื้นที่ที่บางหรือไม่ได้เคลือบจะทำให้ความสามารถในการป้องกันการกัดกร่อนของท่อลดลง
(2) การหยดของสารป้องกันการกัดกร่อน: ปรากฏการณ์นี้สารป้องกันการกัดกร่อนแข็งตัวเป็นหยดๆ บนพื้นผิวท่อ ส่งผลกระทบต่อความสวยงาม แต่ไม่ส่งผลต่อความต้านทานการกัดกร่อนโดยตรง
(3) การเกิดฟองอากาศ: อากาศที่ติดอยู่ภายในสารป้องกันการกัดกร่อนระหว่างการใช้งานจะทำให้เกิดฟองอากาศบนพื้นผิวท่อ ซึ่งส่งผลต่อทั้งรูปลักษณ์และประสิทธิภาพของการเคลือบ
-
การวิเคราะห์ปัญหาคุณภาพการเคลือบ
ปัญหาทุกอย่างเกิดขึ้นจากหลายสาเหตุ เกิดจากหลายปัจจัย และท่อเหล็กมัดหนึ่งที่เน้นคุณภาพของปัญหาอาจเกิดจากหลายสาเหตุร่วมกัน สาเหตุของการเคลือบที่ไม่สม่ำเสมอสามารถแบ่งได้คร่าวๆ เป็น 2 ประเภท หนึ่งคือปรากฏการณ์ที่ไม่สม่ำเสมอที่เกิดจากการพ่นหลังจากท่อเหล็กเข้าไปในกล่องเคลือบ และสองคือปรากฏการณ์ที่ไม่สม่ำเสมอที่เกิดจากการไม่พ่น
สาเหตุของปรากฏการณ์แรกนั้นเห็นได้ง่ายชัดเจน เมื่อนำท่อเหล็กเข้าไปในกล่องเคลือบในมุม 360° จะมีปืนทั้งหมด 6 กระบอก (ท่อปลอกมี 12 กระบอก) สำหรับการพ่น หากปืนแต่ละกระบอกที่พ่นออกมามีขนาดการไหลที่แตกต่างกัน จะทำให้สารป้องกันการกัดกร่อนกระจายตัวไม่สม่ำเสมอบนพื้นผิวต่างๆ ของท่อเหล็ก
เหตุผลที่สองคือมีสาเหตุอื่นๆ สำหรับปรากฏการณ์การเคลือบที่ไม่สม่ำเสมอนอกเหนือไปจากปัจจัยการพ่น มีปัจจัยหลายประเภท เช่น สนิมที่เข้ามาของท่อเหล็ก ความหยาบ ทำให้การเคลือบยากต่อการกระจายอย่างสม่ำเสมอ พื้นผิวท่อเหล็กมีการวัดแรงดันน้ำที่เหลืออยู่เมื่อมีการอิมัลชัน ในครั้งนี้สำหรับการเคลือบเนื่องจากการสัมผัสกับอิมัลชัน ทำให้สารกันบูดเกาะติดกับพื้นผิวของท่อเหล็กได้ยาก ดังนั้นจึงไม่มีการเคลือบส่วนท่อเหล็กของอิมัลชัน ส่งผลให้การเคลือบท่อเหล็กทั้งหมดไม่สม่ำเสมอ
(1) เหตุผลที่สารป้องกันการกัดกร่อนหยดลงมา หน้าตัดของท่อเหล็กเป็นทรงกลม ทุกครั้งที่มีการพ่นสารป้องกันการกัดกร่อนลงบนพื้นผิวท่อเหล็ก สารป้องกันการกัดกร่อนในส่วนบนและขอบจะไหลไปที่ส่วนล่างเนื่องจากปัจจัยแรงโน้มถ่วง ซึ่งจะก่อให้เกิดปรากฏการณ์หยดลงมา ข้อดีก็คือมีอุปกรณ์เตาอบในสายการผลิตเคลือบของโรงงานท่อเหล็ก ซึ่งสามารถให้ความร้อนและทำให้สารป้องกันการกัดกร่อนที่พ่นบนพื้นผิวท่อเหล็กแข็งตัวได้ทันเวลา และลดความลื่นไหลของสารป้องกันการกัดกร่อน อย่างไรก็ตาม หากความหนืดของสารป้องกันการกัดกร่อนไม่สูง ไม่มีการทำความร้อนทันเวลาหลังจากการพ่น หรืออุณหภูมิความร้อนไม่สูง หัวฉีดไม่อยู่ในสภาพการทำงานที่ดี เป็นต้น จะทำให้สารป้องกันการกัดกร่อนหยดลงมา
(2) สาเหตุของการเกิดฟองอากาศป้องกันการกัดกร่อน เนื่องจากความชื้นในอากาศในบริเวณปฏิบัติงาน ทำให้สีกระจายตัวมากเกินไป อุณหภูมิที่ลดลงของกระบวนการกระจายตัวจะทำให้เกิดปรากฏการณ์ฟองอากาศของสารกันเสีย สภาพแวดล้อมที่มีความชื้นในอากาศ อุณหภูมิที่ต่ำกว่า สารกันเสียที่พ่นออกมาเป็นละอองเล็กๆ จะทำให้อุณหภูมิลดลง น้ำในอากาศที่มีความชื้นสูงจะควบแน่นเป็นหยดน้ำเล็กๆ ผสมกับสารกันเสีย และสุดท้ายจะเข้าไปในส่วนเคลือบ ส่งผลให้เกิดปรากฏการณ์ฟองอากาศของสารกันเสีย
เวลาโพสต์ : 15 ธันวาคม 2566